TFF CHARISMA
Underground gas pipeline inspections are currently done manually by walking over the gas line with a sensor. Due to shortage of labor and increasing need for inspection because of new EU regulations Alliander Research Center for Digital Technologies (RCDT) and Smart Mechatronics And RoboTics (SMART) Research Group are working together in this TechForFuture (TFF) project to explore autonomous inspection in the CHARISMA project (CH4 Autonomous Robotized Inspection for Sustainable MaIntenance).
The main research question is: “How to automate robotic inspection of leaks in underground gas pipelines?”
Sub research questions include amongst others:
- How can we integrate a gas sensor with an commercial-off-the-shelf robot for robust gas leakage detection?
- What sensor configurations and technologies are most effective in ensuring accurate and reliable outdoor localization of the robot?
- How accurate can we track gas pipelines within urban environments, incorporating geofencing for enhanced navigation accuracy and safety?
- What strategies can be implemented to ensure the robot's safe interaction with pedestrians, vehicles, and other dynamic elements in urban areas while following gas pipelines?
Background information
A gas leak can be dangerous, wasteful, and harmful to the environment. For these reasons, the EU has made it mandatory to properly inspect and maintain gas networks. In the Netherlands, all pipes must be inspected every 4 years, but some pipes need to be checked more frequently due to higher pressure or different materials.
So far, these inspections have been done entirely by people. However, with limited technical personnel and a steep learning curve for this job, it's hard to inspect often enough. The operator has to walk slowly (3km/h) and gets neck pain from constantly looking down at their tablet. They also risk injuries like a frozen shoulder from pushing the equipment. And let's face it, inspecting gas pipes can get pretty monotonous, especially because the operator may have to walk the same track multiple times.
With a shortage of technicians, Alliander sees a great opportunity for increased robotization. The EU plans to inspect pipes four times a year instead of once every five years. That's 16 times as often! This makes finding a different inspection solution more urgent than ever. That's why Alliander is partnering with Saxion Mechatronics Research Group to develop the CHARISMA project: CH4 Autonomous Robotized Inspection for Sustainable MAintenance. Together, we aim to develop an efficient, safe, and reliable solution that meets the new inspection standards and helps protect the environment.
Project Approach & Goal
Within this project Rapid Learning Cycles (RLC) has been used. This method yields knowledge in timeboxed intervals and involves stakeholders in integration events where important decisions are taken and the course of the future research can be steered.
The core hypothesis in the CHARISMA project is the following:
The CHARISMA Inspection uses a Proof of Principle for reliable and more efficient inspections which is using ROS2 - so that we get knowledge about real-life application of robots in the infrastructure maintenance domain.
The goal of CHARISMA is thus to develop a proof of principle for a robotized system that can automatically detect gas leaks in a robust and reliable fashion. In addition, this project contributes to the Sustainable Development Goals where we improve the work of operators and contribute to lower greenhouse gas emissions.
Research Outcome
This project successfully integrates a Boston Dynamics SPOT robot with a custom built backpack and a Laser Hunter gas sensor by Esders, forming a proof of principle for automated gas pipeline inspections.
The system autonomously detects gas leaks using ROS2 NAV2 with GNSS & RTK for accurate outdoor navigation with a sub-decimeter absolute localization accuracy. A dual antenna configuration provides absolute heading information with high accuracy, eliminating the need for a challenging-to-calibrate and easily disturbed compass.
In addition, the configuration of our navigation stack with the open source ROS2 driver by the Boston Dynamics AI Institute allows SPOT to precisely follow a gas pipeline based on its geo-location. Furthermore, our software configuration offers a simulation environment that facilitates tuning of path planning and locomotion.
The gas sensor is integrated with SPOT via a docker container and ROS2, allowing the robot to detect gas leaks above 1ppm and log the geo-location of the detected leak. As such, the robot is capable of geofencing, e.g. taking pictures of the leak location or physically marking it.
Finally, the custom built backpack offers a cheap and light weight solution to integrate various payloads by providing features such as an onboard PC that is directly interfaced with SPOT as well as several media and power connectors. The backpack will be made available as an open source project.
Subsidized by
Tech For Future (TFF)
In collaboration with
Alliander Research Center for Digital Technologies (RCDT)
Team
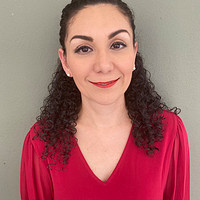
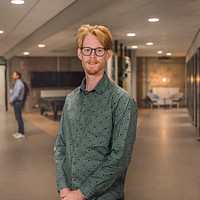