Oude kleren worden nieuwe kleren
Je ruimt je kledingkast op en vindt een broek die eigenlijk niet meer past. Zo’n kledingstuk kun je prima ‘doneren’ aan een textielcontainer voor tweedehands kleren. Maar die trui waar de gaten al in zitten, lijkt rijp voor de prullenbak. Of toch niet? Laura Erkens, docent-onderzoeker bij het lectoraat Sustainable & Functional Textiles, vertelt hoe je van oude kleren nieuwe kleren kunt maken. Een duurzame samenwerking met studenten en het innovatieve bedrijf Wolkat.
Laura Erkens houdt van materialen. Terwijl ze praat over haar onderzoek, dat gefinancierd werd door TechForFuture, gaan oude draadjes en nieuwe kledingstukken door haar vingers. Of eigenlijk gaat het niet om oude draadjes, maar om ‘mechanisch gerecyclede vezels’. Laura pakt een zak met een wollige inhoud, haalt er een plukje uit en trekt het materiaal met haar vingers uit elkaar. “Het zijn vezels gemaakt van afvaltextiel,” vertelt ze. “Oud textiel wordt in stukjes gehakt, vervezelen noemen we dat. Zo wordt het materiaal helemaal losgemaakt. Een oud kledingstuk wordt net zo lang fijngemalen tot je dit hier hebt, en daar kun je dan weer nieuwe garens mee spinnen.”
Het klinkt eenvoudig: onze afdankertjes door de ‘gehaktmolen’, en met de garens die dat uiteindelijk oplevert nieuwe kleding maken. De werkelijkheid is natuurlijk complexer. Voor Laura en het lectoraat Sustainable & Functional Textiles ging het om een zoektocht naar ideale reststromen, de beste machines en de gouden combinatie van gerecyclede vezels en ander materiaal. Dit alles in nauwe samenwerking met Saxion-studenten en Wolkat, een internationaal textielrecyclingbedrijf waar een circulaire werkwijze centraal staat.
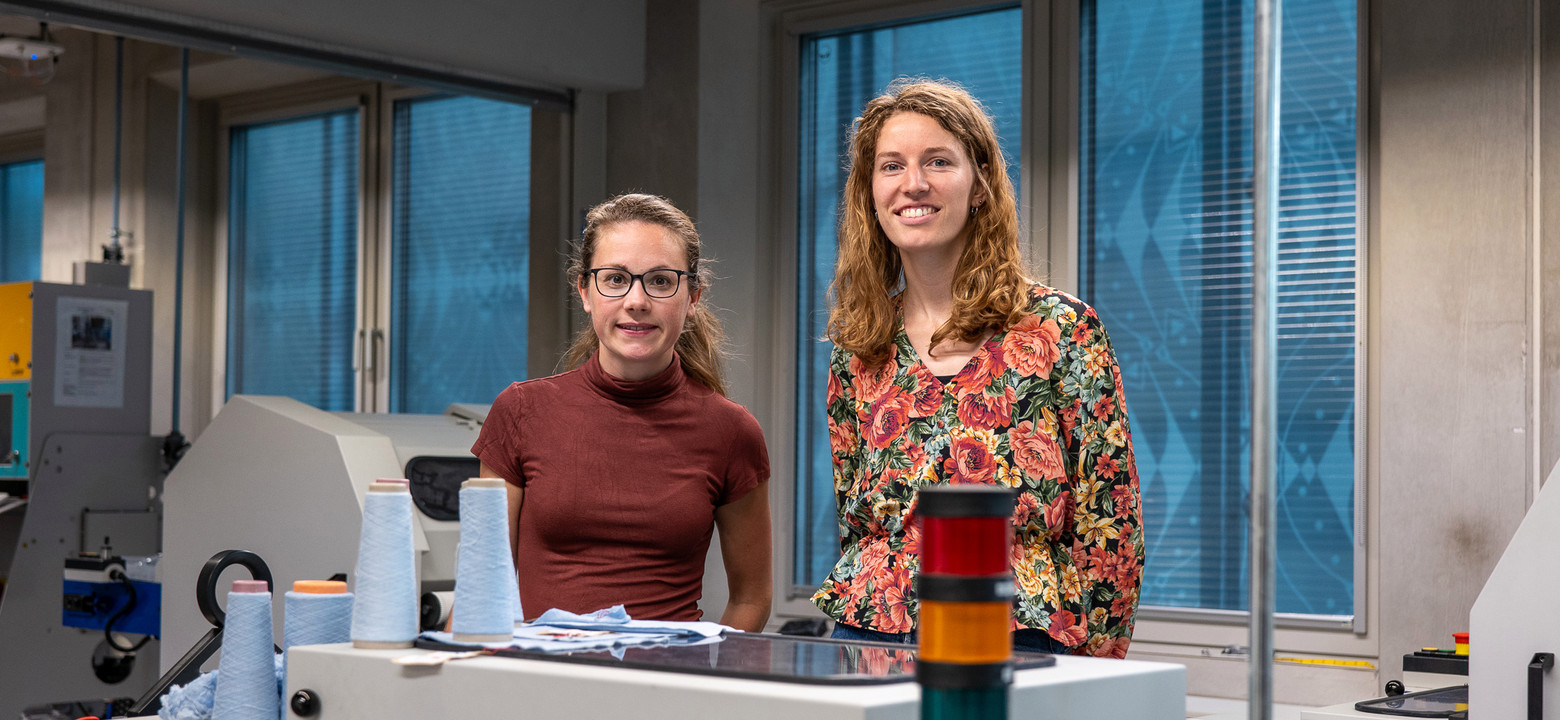
Onderzoekers Laura Erkens en Maud Kuppen in het Circulair Textiel Lab van Saxion. Samen waren Laura en Maud actief binnen het onderzoeksproject dat was gericht op het gebruiken van mechanisch gerecyclede vezels voor het spinnen van nieuwe garens en - uiteindelijk - het produceren van nieuwe kleding.
Liever langdradig
Terug naar de zoektocht en de ideale vezels. Laura vertelt dat hoe langer je oude kleding uit elkaar trekt en vermaalt, hoe fijner het materiaal wordt dat je overhoudt. “Daar zit ook gelijk het probleem,” zegt ze. “In het proces worden de vezels steeds korter, terwijl je het liefst lange vezels wilt.” Om dit toe te lichten, pakt Laura een draad op van tafel. Ze houdt de uiteinden met beide handen tussen duim en wijsvinger, en begint te draaien; de dikkere draad valt uiteen in dunnere draadjes, die om elkaar heen zaten gewikkeld. Van de dunnere draadjes plukt ze probleemloos wat korte, ragfijne vezels. Een iets te snelle ontleding van materiaal waarvan je stevigheid verlangt.
Want het einddoel is duurzame kleding, die voldoet aan allerlei kwaliteits- en milieueisen. Langere vezels hebben meer ‘grip op elkaar’, wat zorgt voor een hogere kwaliteit bij het maken van bijvoorbeeld een T-shirt. Waar de juiste vezellengte een uitdaging is, brengen gerecyclede vezels sowieso voordelen met zich mee op het gebied van milieuvriendelijkheid. “Omdat Wolkat het textielafval dat geschikt is voor recycling op kleur sorteert,” zegt Laura, “heb je geen chemicaliën en water nodig. Het is een droog proces, dus beter voor het milieu.” Wolkat is in dit verband een ideale partner, omdat het bedrijf jarenlange ervaring heeft met textielafvalverwerking en mechanische recycling tot nieuwe garens. “We hebben van Wolkat verschillende vezels gekregen,” zegt Laura, “zowel van vervezelde jeans als gebreide truien. Al die vezels hebben verschillende eigenschappen, die wij beneden in ons Circulair Textiel Lab hebben onderzocht. We hebben gekeken wat je met welke verhouding kan creëren.”
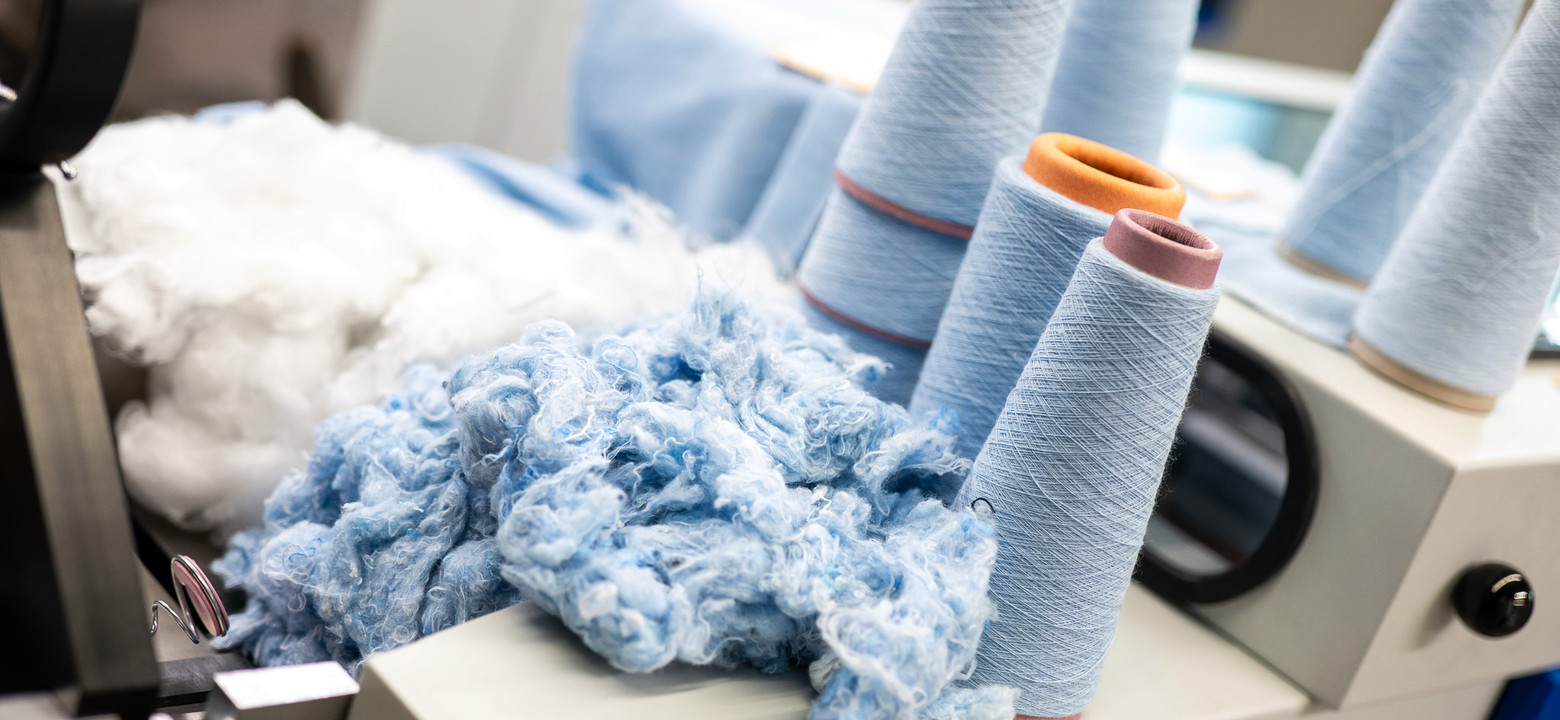
Van de mechanisch gerecyclede vezels van Wolkat werden nieuwe garens gesponnen.
Garen spinnen
Bij het zoeken naar de ideale verhouding, hoorde ook een zoektocht naar het ideale maakproces. “We zijn het gewoon gaan uitproberen,” zegt Laura. “In ons lab bij Saxion hebben we een ringspinmachine staan, maar we hebben ook nog een rotorspinmachine gebruikt van Hochschule Niederrhein in Duitsland. Zo’n andere spinmethode geeft net weer andere resultaten. Toen hebben we de resultaten van al die spinmethoden vergeleken. Bij het rotorspinnen konden we met een iets hoger percentage gerecyclede vezels werken.”
Op de gesprekstafel ligt een klein shirtje, dat Laura zelf heeft gemaakt van het ‘winnende materiaal’. Een materiaal dat voor 55% uit gerecyclede vezels van Wolkat bestaat en voor 45% uit Refibra. Bij Refibra gaat het om een duurzame vorm van lyocell. Ofwel: kunstmatige vezels op basis van houtpulp en 30% chemisch gerecyclede katoen. Deze kunstmatige vezels waren nodig om tot een fijn, bruikbaar garen te komen. Relatief gezien is het resultaat zeker duurzaam; iets waar grote bedrijven best hun garen bij willen spinnen. “Natuurlijk wil je graag naar een eindproduct toe werken,” zegt Laura. “Daarom hebben we ook de samenwerking met HEMA gezocht. Als een soort case hebben we toen een T-shirt en een overhemd van HEMA genomen – een T-shirt is gebreid en een overhemd geweven – en daardoor konden we twee verschillende textielsoorten vergelijken. Ook hebben we vanuit HEMA de kwaliteitseisen gekregen die zij aan hun producten stellen.”
Naast alle voordelen op het vlak van duurzaamheid, zagen we – toen we keken naar commerciële haalbaarheid – dat een hoog percentage mechanische gerecyclede vezels ook de kostprijs ten goede komt.
Van het lab naar de schappen
Met die kwaliteitseisen gingen Laura en haar team weer het lab in. Alle resultaten die tot dan toe in het onderzoek waren behaald, werden aan de eisen van HEMA onderworpen. Dit met de hulp van Saxion-studenten. “Eén student heeft met het gerecyclede garen verschillende breitesten gedaan,” zegt Laura. Ze pakt een ander kledingstuk op en vervolgt: “Je ziet het, allemaal gaten, dus dat ging niet direct vlekkeloos. Vervolgens hebben we specifieke testen gedaan, bijvoorbeeld met het oog op slijtage.” De studenten die meedraaiden in het project, hebben hun handen volop uit de mouwen gestoken: van spinnen, weven en breien tot het uitvoeren van diverse tests in het textiel-lab.
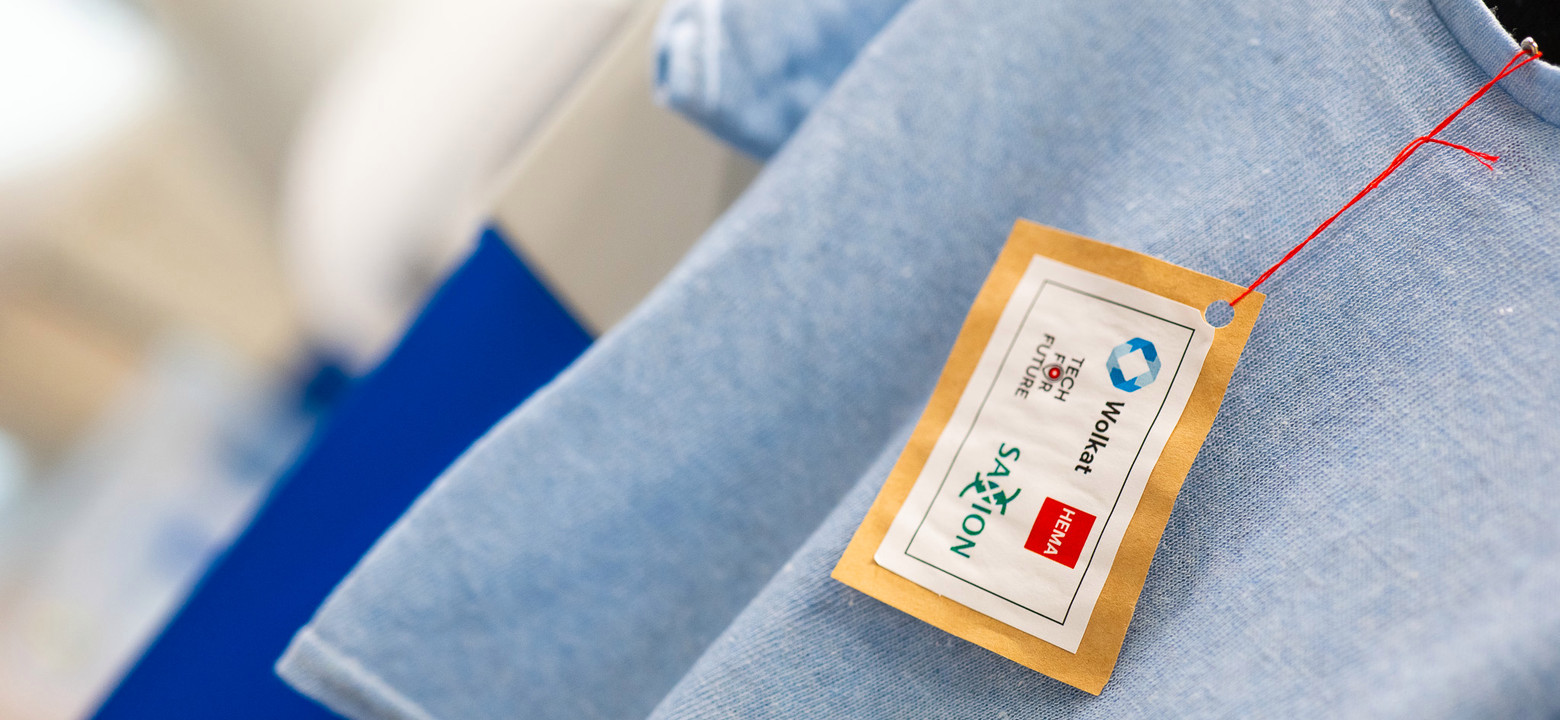
Shirtje dat onderzoeker Laura Erkens zelf heeft gemaakt van garens op basis van mechanisch gerecyclede vezels. De gebruikte garens bestaan voor 55% uit gerecyclede vezels van Wolkat en voor 45% uit Refibra.
Op dit moment liggen de onderzoeksresultaten van het lectoraat Sustainable & Functional Textiles nog niet in de schappen van Nederlandse warenhuizen. Hoewel er in de praktijk al kleding wordt verkocht die voor een klein percentage bestaat uit gerecyclede garens, is de stap naar kleding die voor meer dan de helft uit circulair materiaal bestaat voor de industrie nog te groot. “Dat is best nog wel lastig,” licht Laura toe. “Omdat er een fijner garen nodig is dan op dit moment wordt geproduceerd. En fijn garen is het lastigst om te maken. Wat we gezien hebben op basis van de testen die we hebben gedaan, is dat het vezelmateriaal van Wolkat kwalitatief gezien prima is. Naast alle voordelen op het vlak van duurzaamheid, zagen we – toen we keken naar commerciële haalbaarheid – dat een hoog percentage mechanische gerecyclede vezels ook de kostprijs ten goede komt.” En wat is de volgende stap? Laura: “Wij hebben alles op lab-schaal gedaan. Wolkat gaat in het najaar kijken of zij dit in hun fabriek ook op grotere schaal kunnen toepassen.”
Fotografie: Thomas Busschers